When residents wanted a custom-made master staircase railing for their East Hampton house a few years ago, they were looking for what would become a centerpiece. They got it in the form of a curved elliptical staircase with custom balusters and finish.
“Everything was designed with that staircase in mind,” Rachel Miller, president of Spirit Ironworks in Bayport, says of the railing that took eight months from design to completion. “It’s the focal point.”
Rachel and Tim Miller, a brother and sister team who run Spirit Ironworks, do fine metal work, including blacksmithing, which entails metalwork to create objects primarily from wrought iron or steel, but sometimes from other metals.
When people want miracles in metal, including heavenly staircases, the Millers are among the master metalworkers who provide it. “
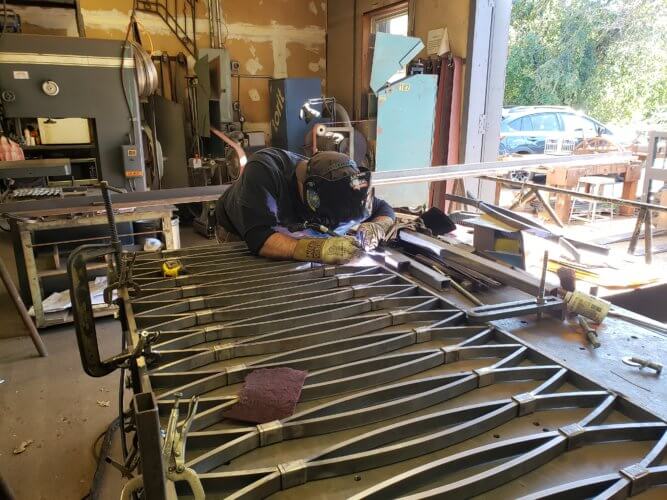
The balusters and railing were curved,” Tim, a master craftsman, says of that particular staircase. “They wanted a bright finish. It was bare metal. Everything had to be polished and sanded.”
The brother and sister team also designed and built a stainless steel staircase with a custom railing and a fireplace screen from hand-hammered stainless steel for a home in Southampton.
“That’s a hard material to work with,” Rachel says. “And it was a unique design.”
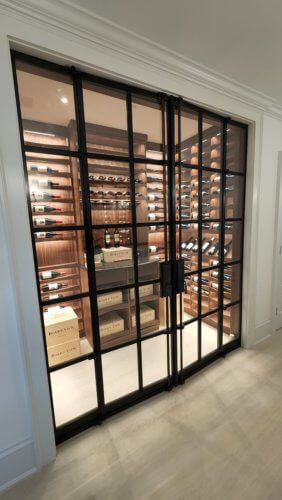
Tim described a 14-foot-tall door they made, along with a fireplace surround and driveway gate, for a house in Southampton.
“Everything we make is handmade, a lot of times using traditional methods,” Tim says. “And it’s one of a kind.”
A tour of their metal-working shop reveals finely crafted metal filigree, metal pieces showcasing finishes, steel flowers given a hand finish with graphite and mica powder and even a bright, fragile-looking flower covered with gold leaf.
“Stainless steel is popular,” Rachel says. “People are in love with custom patinas, blackened steel. You put a chemical on the steel to make it look older. We do the same thing with bronze.”
They crafted a door with 12 bronze portholes and corrugated stainless steel paneling, which they sent to a company to help exactly match bronze hardware in the home. “Sometimes those are the lengths you go to, to get the desired effect,” Rachel says.
They walked Behind The Hedges through their studio, a veritable metalworking museum showcasing work they do for residences, businesses, restorations and art installations.
“This is a sample for a driveway gate we did in North Sea for a private gated community,” Rachel says as she walks through the studio.
The two grew up with metals: Their father, Harry Miller, owns Miller’s Mint, a coin store in Patchogue, where they were introduced to heating and working metal. At age 11 on a visit to the Bellport-Brookhaven Historical Society’s blacksmith shop, Tim saw a blacksmith cutting hot steel with a chisel.
“For some reason, that image was seared into my memory. The idea that hard, cold metal could be shaped in heat with a hammer and anvil blew my 11-year-old mind,” he says. “I was interested in tools and history and fire. The idea that you could create something using fire was appealing to me.”
The siblings later obtained permission to work in that same shop. Tim received a BFA in metals in 1998 from SUNY New Paltz; in 1999 he set up his own forge in Bayport and founded Spirit Ironworks in 2001. Rachel obtained a B.F.A. in 1992 from the University of the Arts in Philadelphia.
“It’s basically when you take something of yourself and put it into the work,” Rachel says of naming Spirit Ironworks. “You take part of your spirit and put it into your work.”
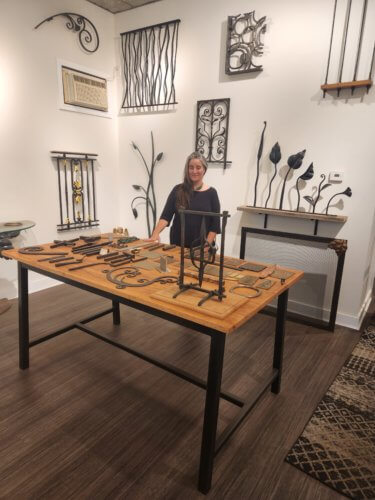
They say it takes years to build the necessary skills by reading books, taking classes at craft schools with other experienced blacksmiths, as well as online discussions in professional forums.
“We started out as artists and we wanted to continue to make art. This is a vehicle to do that,” Rachel says. “There were times 500 years ago when very wealthy people became patrons of the arts. In a way, some of our clients are like that when they request a unique piece.”
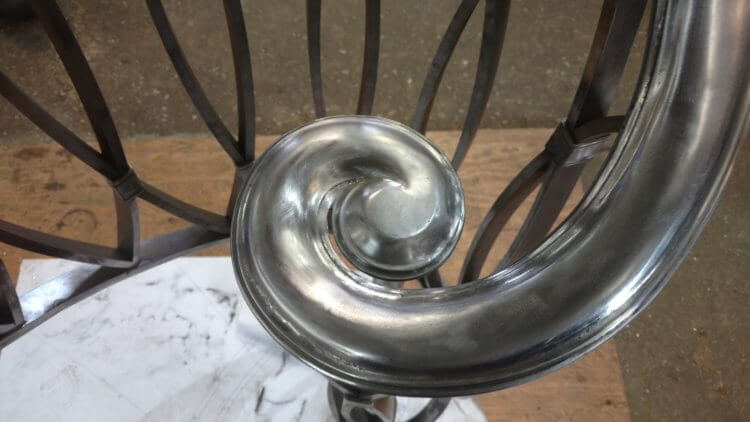
of the master stair railingCourtesy of Spirit Ironworks
At first they both did metal work; now Tim leads the metal work, while Rachel oversees the business itself.
“We’ve been in business almost 20 years. For about the first half, I worked in the shop,” Rachel says. “As our jobs became more complex, someone needed to run the front end of the business.”
They walk around their 5,000-square-foot shop with fans running, stopping in the blacksmithing area near two coal forges for heating and shaping metal. There are also two power hammers and a gas forge in the shop that employs eight workers.
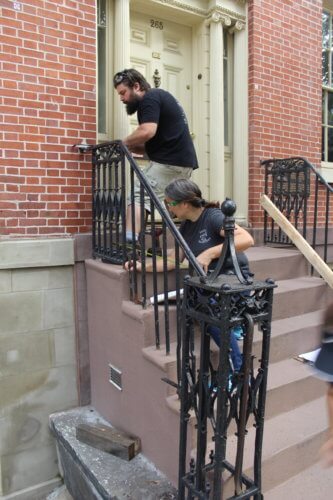
for removal and complete restoration.Courtesy of Spirit Ironworks
“These are feathers for a large sculpture we’re making,” Tim says of work for a developer to go up near the Wyandanch railroad station. “We have some unique equipment that allows us to shape big pieces of sheet metal.”
They also do historical restoration, including restoring a 15-foot weathervane for the Vanderbilt Museum and Planetarium in Centerport.
“There are a lot of rusted parts. We’re replacing that with new,” Rachel says. “A big globe goes on the bottom of this weathervane. We’re going to restore that.”
They made a 45-pound, wrought iron bell clapper as part of a work for a Jeff Koons retrospective at the Whitney Museum of American Art in Manhattan.
The company does custom fabrication, blacksmithing, art, and restoration, mixing tradition with new technology, including an induction forge that heats metal through magnetism.
“This is a way of heating metal that has become affordable and accessible,” Tim says of the equipment that turns metal rods bright orange amid 2,000-degree heat. “It uses an oscillating electromagnetic field to create electrical currents inside the metal. We use that when we need a small area heated up or we have a bunch of small parts to make.”
They recently used that to make custom nails for a house in Saint Kitts, as they match the machine to the task. Tim approaches a large hydraulic cylinder mounted to a welding table.
“This is a machine we built on our own to bend metal,” he says. “We can use it for cold bending metal without heating.”
While to many people blacksmithing may be a thing of the past, Tim says it remains a vibrant craft.
“I think there was really a need for us,” he says. “But there wasn’t an awareness that this was something people were still willing to do.”
This article appeared on the cover of Behind The Hedges for October. Read a digital version of the magazine in Dan’s Papers here, as well as the issue that appeared in the Long Island Press.
Read past Master Craftsman columns here. Have someone to suggest for the column? Email TVecsey@danspapers.com.
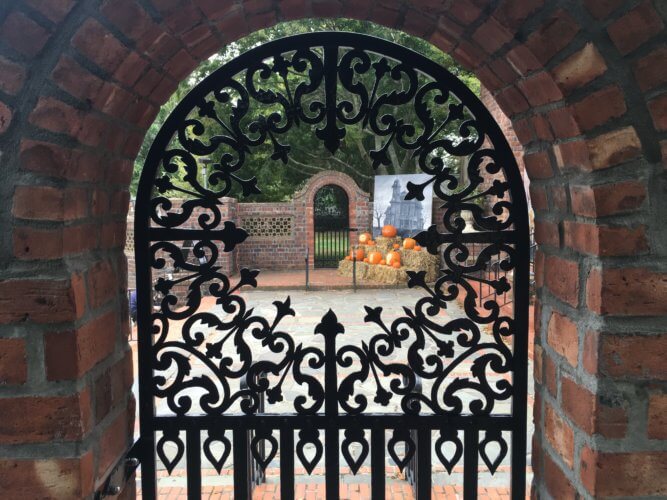
at the Southampton Arts CenterCourtesy of Spirit Ironworks